5 facts on welding machine parts
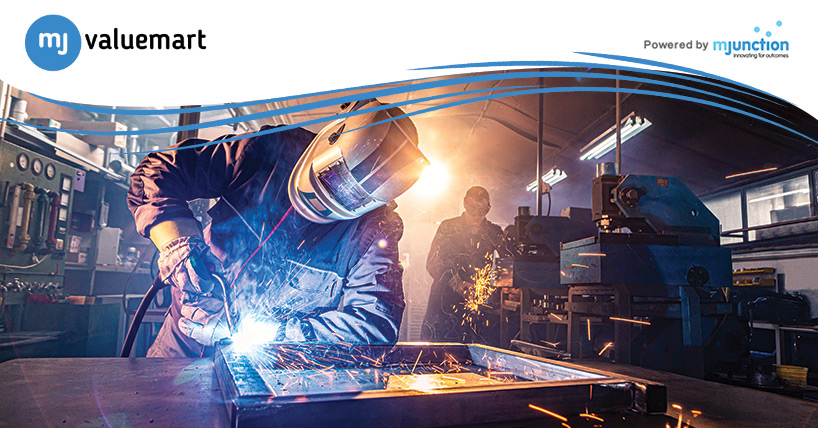
Welding machines are very important tools used in different industries. They are used for joining two or more pieces of metal together by using heat and pressure. These machines consist of several important parts that work together to facilitate the welding process. If you are searching for useful insights on welding machine parts, here is a good read:
1. The power source provides the electrical energy needed for welding. It may be a transformer, inverter, or generator, depending on the type of welding machine. When selecting a power source, factors to consider include efficiency, power output, ease of use, and compatibility with specific welding needs. One factor to consider is whether a constant current (CC) or constant voltage (CV) power source is required. CC machines maintain a steady current while varying the output voltage, while CV machines fluctuate the output current while maintaining a set voltage. CC machines are useful for applications where the welder needs to control the arc length manually, as the current reaching the material remains constant regardless of the arc distance. On the other hand, CV machines are important for Gas Metal Arc Welding (GMAW) and Flux Cored Arc Welding (FCAW), where the arc length is not controlled manually.
2. A ground clamp, also referred to as an earth clamp or work clamp, is one of the important welding machine spare parts in India. It establishes a reliable electrical connection between the workpiece being welded and the ground terminal of the welding machine. The ground clamp is typically constructed from conductive materials to ensure a low-resistance path for the electrical current. It is designed with a strong spring-loaded mechanism that securely holds onto the workpiece, ensuring good electrical contact. The clamp is attached to the welding machine with a flexible cable. This lets the electrical current move from the machine, through the clamp, and into the workpiece. This completes the electrical circuit that is needed for welding.
3. The gas regulator in welding processes, such as MIG or TIG welding, controls the flow of shielding gas. It ensures a consistent and controlled flow of gas from the gas cylinder to the welding torch or nozzle. The gas regulator is typically connected to the gas cylinder using a pressure-resistant hose. It contains a pressure gauge to indicate the pressure inside the cylinder and a flowmeter or flow control valve that allows the welder to adjust and maintain the desired flow rate of the shielding gas. By regulating the flow of gas, the gas regulator creates a protective atmosphere around the welding arc, preventing oxidation and contamination. This protective shield of gas is crucial for producing high-quality welds. The gas regulator plays a crucial role in precise gas control and is essential for achieving optimal welding performance.
4. Consumables in welding machines are materials that are used up during the welding process. They are important for facilitating the welding operation and ensuring good-quality welds. Common consumables include electrodes, filler metals, shielding gas, and fluxes. Electrodes are used in arc welding, while filler materials add substance to welding joints. Shielding gas is typically used in MIG and TIG welding and is consumed when the welding torch is ignited. Fluxes are utilised in processes like flux-cored arc welding and submerged arc welding.
5. A cooling system in welding machines is designed to regulate and dissipate heat generated during welding processes, preventing the machine from overheating. Cooling systems commonly use cooling fans and radiators to remove heat from the welding machine. Cooling fans circulate air to remove heat from internal components, such as transformers and electronic circuits. Radiators provide additional cooling by transferring heat to the surrounding environment through heat exchange. Some advanced welding machines may utilise water-cooling systems as well.
Each one of the aforementioned welding machine parts are crucial for the proper functioning of the equipment. If one or more of them malfunctions, you will need to quickly identify and replace the said parts. Failure to do so may cause delays in operations and lead to losses.